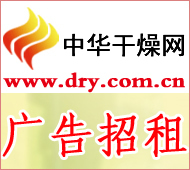
It is understood that the solution polymerization technology is Daqing Petrochemical Company's own technology that was transformed and formed on the basis of nickel solution polymerization technology. It is superior to Japanese technology in catalyst composition, catalyst aging, solvent and solvent recovery. This technology uses 1,3-butadiene as a monomer to refinery refinery raffinate 60 °C ~ 90 °C fraction solvent, naphthenic nickel acid, triisobutyl aluminum, boron trifluoride etherate network The compound is a catalyst for solution polymerization. The production process is mainly composed of raw material storage, chemical agent preparation, continuous polymerization, condensation, drying, molding, solvent and butadiene recovery.
After several technical improvements, the current nickel solution polymerization technology of Daqing Petrochemical has formed its own technical characteristics, which has attracted the attention of foreign counterparts. In the preparation of polymerization units, a new catalyst premix production process has been added, which has changed the aging method of the catalyst and the feeding mode, and improved the utilization efficiency, activity and stability of the catalyst; on the agglomeration unit, the heat pump system and alkali have been added. The tower is washed to recover the thermal energy from the top of the agglomerating tank to reduce the steam consumption and reduce the corrosion of the solvent to the rear system. The condensed mode was changed from overflow differential pressure operation to pump differential pressure operation, which is conducive to recovery of solvent oil and energy saving. Pre-coagulating facilities were added to reduce the consumption of solvent oil and steam; in the solvent recovery unit, the operation flow was optimized, and a nitrogen recovery system was added, which further saved energy consumption and material consumption. In addition, high-efficiency trays are also used to improve the processing capacity and separation efficiency of the recycling system.
At present, most of the world's butadiene rubber plants are produced by solution polymerization. The solvents used are raffinate, benzene, toluene, heptane, n-hexane, and cyclohexane. The catalysts used are cobalt, titanium, lithium, nickel, and rare earth. Department. China's butadiene rubber used raffinate as solvent, nickel naphthenate, boron trifluoride etherate and triisobutyl aluminum as catalysts, and later realized industrial production of lanthanide rare earth butadiene rubber.
Cas 61788-45-2,Tallow Amine Structure,Tallow Amine 61788-45-2,Hydrogenated Tallow Alkyl Amines
Sichuan Yibin United Import & Export Ltd. , https://www.ybund.com