1 Overview The general trend of the development of machining is high efficiency, high precision, high flexibility and enhanced environmental awareness. In the field of machining, cutting (grinding) is the most widely used machining method. High-speed cutting is the development direction of cutting machining and has become the mainstream of machining. It is an important common key technology for advanced manufacturing technologies. The promotion and application of high-speed cutting technology will greatly increase production efficiency and processing quality and reduce costs. The development and application of high-speed cutting technology is determined by the advancement of machine tools and tool technology, in which the progress of tool materials plays a decisive role. Studies have shown that during high-speed cutting, as the cutting speed increases, the cutting force decreases, and the cutting temperature rises very high. After reaching a certain value, the increase gradually slows down. The main cause of tool damage is the abrasion and damage of mechanical friction, bonding, chemical wear, chipping, crushing, and plastic deformation under the action of cutting force and cutting temperature. Therefore, the most important requirement for high-speed cutting tool materials is high temperature. Mechanical properties, thermophysical properties, anti-adhesion properties, chemical stability (oxidation, diffusion, solubility, etc.) and thermal shock resistance, and resistance to coating cracking. Based on this requirement, in the past 20 years, a number of tool materials suitable for high-speed cutting have been developed, and various workpiece materials can be machined under different cutting conditions. At present, high-speed cutting of aluminum alloys (Si content ≤12%, greater than 12% for 500 to 1500m/min) can be performed at 2500 to 5000 m/min. Cutting of cast iron at 500 to 1500 m/min: 300 to 1000 m/min Cutting steel: 100 ~400m/min cutting hardened steel, heat-resistant alloy: 90 ~ 200m/min cutting titanium alloy. Of course, people also look forward to processing at ultra-high cutting speeds for better results. 2 The progress and application of foreign high-speed cutting tool materials in foreign countries When high-speed cutting is performed, the best cutting results can only be achieved by selecting different tool materials and permissible cutting conditions for different workpiece materials. Accordingly, for the high-speed cutting of aluminum alloys, cast irons, steels and alloys and heat-resistant alloys that are widely used in production, the developed tool materials mainly include: diamond, cubic boron nitride, ceramic tools, coated tools, and TiC. (N) Base carbide cutting tools (cermet) etc. Diamond cutters Diamond cutters are divided into natural and synthetic diamond cutters. Natural diamond has the highest hardness and thermal conductivity in nature. However, due to the high price, processing and welding are very difficult. Except for a few special applications (such as watch precision parts, lighting accessories and jewelry engraving and other processing), it is rarely used as a cutting tool in the industry. With the development of high-tech and ultra-precision machining, such as miniature parts of micromachines, various reflectors in nuclear reactors and other high-tech fields, navigation gyros in missiles or rockets, ultra-precision parts such as computer hard disk chips and accelerator electron guns. Processing, single crystal natural diamond can meet the above requirements. In recent years, a variety of methods for chemically grinding diamond cutting tools and brazing diamonds in protective atmospheres have been developed, making it easier to manufacture natural diamond cutting tools. Therefore, in the field of high-tech applications for ultra-precision mirror cutting, natural diamonds have played a role. Important role. In the 1950s, after artificial diamond powder was synthesized using high-temperature and high-pressure technology, a diamond-based cutting tool, ie, polycrystalline diamond (PCD), was manufactured in the 1970s. PCD grains were arranged in an unordered state and had no directionality, resulting in uniform hardness. It has high hardness (8000 ~ 12000HV) and thermal conductivity, low coefficient of thermal expansion, high modulus of elasticity and low coefficient of friction, very sharp edges. It can process a variety of non-ferrous metals and wear-resistant high-performance non-metallic materials, such as aluminum, copper, magnesium and its alloys, carbide, fiber plastic materials, metal matrix composites, wood composite materials. The average size of the diamond grains contained in the PCD tool is different, and the impact on the performance is also different. The larger the grain size, the higher the wear resistance. With similar edge processing, the smaller the grain size, the better the edge quality. For example, a PCD tool with a grain size of 10-25 μm is used to process aluminum alloys with a Si content of less than 12% with a PCD with a high speed grain size of 8 to 9 μm ranging from 500 to 1500 m/min, PCD with a grain size of 4 to 5 μm, and plastic. Wait. For ultra-precision machining, PCD tools with a small grain size should be used. Usually PCD cutters are sintered into diamond-carbide composite inserts for welding on the body. Using ultra high pressure devices, single crystal diamonds with neat shapes and very few impurities can be artificially synthesized at high temperatures ranging from 5 to 60,000 atm and 1400 to 1,600°C. The quality is uniform and stable, and the crystal surface is very clear and easy to identify. It has the highest thermal conductivity of all materials and the same strength as natural diamond. The current maximum size is 8mm. The good uniformity of the size, shape and performance of this single crystal diamond is not achievable in natural diamond products. It has better wear resistance than PCD. When the wear resistance of PCD exceeds 700 °C, it will be weakened, because its structure contains metal Co, which promotes "reverse reaction", that is, the transition from diamond to graphite. However, it has good fracture toughness and can be interrupted. For example, an aluminum alloy having a Si content of 10% can be end milled at a high speed of 2500 m/min. At present, the application of artificial synthetic single crystal diamond tool materials has been rapidly developed, and its new application area is the wood processing industry. There is an increasing demand for highly wear-resistant laminate flooring with aluminum oxide coating. During the processing, the wear-resistant layer of the wood will cause the blade to be passivated, resulting in the cracking of the alumina wear layer, and the blade must be sharpened or replaced. However, the performance of the artificial single crystal diamond is significantly better than that of the PCD tool. Currently, chemical vapor deposition (CVD) diamonds are being researched and developed, and PCDs with excellent intergrown growth have been deposited. They have a columnar structure and are very dense. With different growth conditions, CVD diamond also exhibits different grain sizes and structures. It does not require a metal catalyst, so its thermal stability is close to that of natural diamond. According to different application requirements, different CVD deposition processes can be chosen to synthesize PCDs with large differences in grain size and surface morphology. CVD diamond as a tool requires a variety of different grain sizes because of its different applications. CVD diamond is made in two forms: one is the deposition of a thin film (CVD film) on the substrate with a thickness of less than 30 μm: the other is the deposition of a substrateless diamond thick film (CVD thick film) with a thickness of 1 mm. Currently, CVD thin film diamonds are not widely used. The CVD thick film can be brazed to the substrate by special but easy-to-follow techniques, but the strength of the solder joints must be guaranteed. Compared with PCD, it has good thermal stability but high brittleness and is not electrically conductive. Cannot be used in EDM technology. CVD thick film diamond has been widely used in woodworking tools and dressing tools. Due to the high purity and high wear resistance and thermal stability of CVD thick film diamonds, there is great potential in the field of high speed machining of high wear resistant materials. The CVD thick diamond cutting tool material currently available for EDM cutting has also been successfully manufactured, and it has yet to be tested and evaluated. The current cost of CVD thick-film diamond is higher. With the development of technology, the cost is gradually reduced. It will be a powerful competitor to PCD. The performance characteristics of PCD, CVD thick film and synthetic synthetic single crystal diamond for the three main diamond tool materials are: PCD weldability, mechanical grinding and fracture toughness are the highest, abrasion resistance and edge quality are medium, corrosion resistance Worst. The CVD thick film has the best corrosion resistance, mechanical grindability, edge quality, and fracture toughness and wear resistance centered, and poor weldability. Synthetic single-crystal diamond edge has the best wear resistance and corrosion resistance, and its weldability, mechanical grinding ability and fracture toughness are the worst. Diamond cutter is the ideal tool material for high speed cutting (2500-5000m/min) aluminum alloy, but due to the affinity of carbon on iron, especially at high temperature, diamond can react with iron chemically, so it is not suitable for cutting. Iron and its alloy workpieces. Cubic Boron Nitride Cubic Boron Nitride (CBN) is a purely synthetic material. It is a second superhard material, CBN micropowder, synthesized in the late 1950's using a diamond-like method. Due to the poor sintering properties of CBN, it was not until the 1970s that cubic boron nitride sintered compacts (polycrystalline cubic boron nitride PCBN) were produced, which consisted of CBN fines with a small amount of binder phase (Co, Ni or TiC, TiN, Al2O3). ) Sintered at high temperature and pressure. CBN is a dense phase of boron nitride, with high hardness (second only to diamond) and heat resistance (1300 to 1500°C), excellent chemical stability (better than diamond) and thermal conductivity, low coefficient of friction . The affinity between PCBN and Fe elements is very low, so it is an ideal tool material for high-speed cutting of ferrous metals. The PCBN microstructures are arranged in disorder with uniform hardness, no directionality, consistent wear resistance and impact resistance, and overcome the shortcomings of CBN easy cleavage and anisotropy. CBN content, grain size, and adhesion will affect the performance of PCBN. CBN content is high, PCBN hardness and thermal conductivity is high, CBN grain size is large, its resistance to damage is weak, the sharp edge of the blade is poor, when the metal material Co, Ni is used as the binding phase, PCBN has better toughness and conductivity When the ceramic material is used as the binder phase, it has better thermal stability. At present, PCBN layers of about 0.5mm are directly sintered or brazed on a cemented carbide substrate to make a PCBN composite sheet, which is advantageous for improving the strength, solderability, and ease of manufacturing PCBN tools. There are roughly two types of PCBN blanks in terms of organization. One is a high content of PCBN (CBN, mass of 80% to 90%), mainly consisting of direct bonding between CBN grains, with high hardness and high thermal conductivity. The other is PCBN with a low CBN content, which is firmly bonded with a small amount of metal or ceramic binder and has good strength and toughness. Generally lower CBN content (50% to 65%) of PCBN tools is suitable for finishing 45 to 65HRC hardened steels, high content (80% to 90%) suitable for processing nickel-chromium cast iron, coarse and semi-rough Cutting of hardened steel, high speed cutting of cast iron, machining of hard alloys, sintered metals and heavy alloys. Choosing the right PCBN tool for CBN content can process cast iron at 500 to 1500m/min at high speed, 45 to 65HRC for hardened steel at 100 to 400m/min, and heat-resistant alloy at 100 to 200m/min. However, steels and alloy steels, alloy cast irons, and heat-resistant alloys that are not suitable for ferritic steels and 45HRC or less are not suitable for machining. In particular, workpieces below 35HRC are not suitable for processing. Coating CBN tools are still under study. Ceramic Tools Ceramic tools are one of the most important tool materials for high-speed cutting. At present, the proportion of ceramic inserts in various countries is about 3% to 5% in the United States, 5% to 7% in Russia, 7% to 9% in Japan, 9% to 12% in Germany, the United Kingdom, France, and Sweden. Also strongly promote the application. Due to the great progress made in the raw materials, components, and preparation processes of modern ceramic cutting tools, sales of ceramic cutting tools have increased by 20% in the past five years. The internationally developed ceramic cutting tools are mainly alumina-based (Al2O3) and silicon nitride-based (Si3N4) series. Adding a variety of oxides, nitrides, carbides, borides to form different types of Alumina-based and silicon nitride-based ceramic cutters. There are more than 40 varieties and more than 200 brands, among which there are more than 25 kinds of alumina bases and nearly 15 kinds of silicon nitride bases. Ceramic cutters have high hardness and wear resistance, hardness of 93 ~ 95HRA, good wear resistance, suitable for processing 50 ~ 65HRC high hardness materials, such as chilled cast iron and hardened steel. High temperature performance, cutting at 1200°C. With good anti-adhesive properties, Al2O3 has a low affinity with metals, and it has a lower reactivity with many metals than many carbides, nitrides, and borides. It is not easy to bond with metals and has good chemical stability. The dissolution rate of Al2O3 in iron is about 1/5 of that of WC, and the diffusion wear is small. The oxidation resistance of Al2O3 is particularly good. Even if the cutting edge is in a hot state, it can be used continuously for a long time and is suitable for high-speed cutting. Ceramic tools also have a lower coefficient of friction than cemented carbide. The main disadvantages of Al2O3-based ceramic tools are lower strength and fracture toughness, greater brittleness, poor thermal conductivity, and low thermal shock resistance. However, for decades, a lot of effective research work has been done to improve the mechanical properties of ceramic cutting tools. For example, hot pressing and hot isostatic pressing processes are used, and various toughening and reinforcing phases are added. For example, metal carbides are added to Al2O3, Nitrides, borides and pure metals and whiskers, such as Al2O3 + TiC, Al2O3 + ZrO2, Al2O3 + SiCw (whisker), Al2O3 + TiN, Al2O3 + TiCN, etc., some add a small amount of Mo in these combined ceramic tools , Ni and other metals and rare earth elements improve the performance of ceramic cutting tools. Alumina-based ceramic tools can cut steel, cast iron and its alloys at high speed, and Al2O3+SiCw is suitable for machining nickel-base alloys. Silicon nitride (Si3N4)-based ceramics and Al2O3-based ceramics, the most significant feature is the higher strength and fracture toughness, low thermal expansion coefficient, low elastic modulus, so its thermal shock resistance is high. Si3N4-based ceramic tools are suitable for machining cast iron. Continuous and interrupted cutting are superior to Al2O3-based ceramic tools. They can also be used for finishing and semi-finishing high hardness materials such as chilled cast iron and hard rolls. However, due to its chemical affinity with iron significantly exceeds that of Al2O3-based ceramics, chemically generated low-melting compounds cause the cutting edge to fail in a short time. Therefore, Si3N4-based ceramic cutting tools are much worse than Al2O3-based steels. Si3N4 based ceramic cutting tools also incorporate various toughening and reinforcing phases in Si3N4 to form a variety of ceramic tools. Si3N4-Al2O3 (Sialon) ceramic cutting tool is a new type of ceramic cutting tool. It is based on Si3N4 by replacing part of nitrogen in Si3N4 with oxygen and partially replacing aluminum with silicon. It is developed by Si-Al. -ON Generic term for various compound groups of various compositions. Sialon ceramic tools have higher strength and fracture toughness, chemical stability, oxidation resistance and high temperature creep resistance, high thermal conductivity, and small thermal expansion coefficient, so they have high thermal shock resistance. Due to its high creep strength, there is no obvious increase in damage due to plastic deformation when the tool tip is subjected to repeated high stress and heat. It is excellent for high-speed roughing of cast iron and nickel-base alloys. Tool material. The whisker-toughened ceramic knives are superior in difficult-to-machine materials such as precision-finishing semi-finishing cars and nickel-base alloys. The Sialon ceramic tool is more adaptable during roughing and milling, but its dissolving wear rate is much higher than that of Al2O3-based ceramic tools and is thus not suitable for machining steel parts. The ceramic cutting tool can select 500-1000m/min high-speed cutting cast iron, cutting the steel with a speed of 300-800m/min, and cutting high-hard material (50-65HRC) with a speed of 100-200m/min. Cutting heat-resistant alloys at speeds up to 300m/min. The main components of the TiC(N)-based hard alloy TiC(N)-based hard alloy are TiC (titanium carbide), TiN (titanium nitride), and TiCN (titanium carbonitride), which are highly wear-resistant TiC. +Ni or Mo, highly ductile TiC+WC+TaC+Co, tough TiN as the main body, and high-strength and tough TiCN+NbC-based TiC(N)-based hard alloys. Compared with WC cemented carbide, hardness, strength, toughness, resistance to plastic deformation and chipping resistance have been significantly improved, mainly due to the increase in high temperature strength, high temperature hardness, thermal conductivity, oxidation resistance and thermal shock resistance. Steel has a low affinity, a small friction coefficient, anti-crater wear and anti-adhesive ability, has now developed into a separate series of tool materials. In recent years, TiC(N)-based hard alloys with high nitrogen content and uniform fine and hard microstructure have been developed. They are suitable for cutting general steels at high speeds of 200-400 m/min due to good wear resistance and chipping resistance. Alloy steel can also be used for the finishing of cast iron. Coating tools for coating tools have developed rapidly, and over 80% of them are currently coated tools. Widely used is the application of different nitrides, oxides, and borides on cemented carbide and high-speed steel bodies, among which aluminum oxide (Al2O3), titanium carbonitride (TiCN), titanium aluminum nitride (TiAlN) , Aluminum titanium aluminum nitride (TiAlCN), etc., have excellent high temperature properties. From a single coating to a multi-coating, the coating processes are chemical vapor deposition (CVD) and physical vapor deposition (PVD). The PVD method is mainly used for high speed steel tools, and the CVD method and PVD method can be used for the coating of cemented carbide tools. The PVD carbide cutting tool has good resistance to breakage and is suitable for intermittent cutting, but its wear resistance is not as good as that of CVD carbide cutting tools. Coated tools vary in properties depending on the coating material. Coated carbide tools have: high hardness and wear resistance (2100-4200HV), high heat resistance (1000-1200°C), high resistance Bonding properties, high chemical stability and low coefficient of friction, excellent WC-based, TiC (N)-based hard alloys and ceramics can be used as a matrix coating tool. At present, the coating materials for high speed cutting coated cemented carbide tools mainly include CVD TiCN+Al2O3+TiN, TiCN+Al2O3, TiCN+Al2O3+HfN, TiN+Al2O3 and TiCN and PVD composite coating TiAlN/TiN. , TiAlN, etc. Single-coated TiC or TiN is no longer needed. The choice of coated cemented carbide tools with different coating materials can process steels, alloy steels, stainless steels, cast irons and alloyed cast irons at speeds of 200 to 500 m/min. In recent years, carbon nitrides (CNx), nitrides (TiN/NbN, TiN/VN), etc. have been developed to have good thermal stability at high temperatures and are suitable for high-speed cutting. Soft-coated tools (such as MoS2, WS2 coated high-speed steel tools) are mainly used to process high-strength aluminum alloys, titanium alloys, or precious metals. Japan's recently developed nano-TiN/AlN composite coating milling inserts with 2,000 coats, each with a thickness of 2.5 nm, can be cut at high speeds. At present, complex tools (drills, gear cutters, broaches, etc.) are mainly coated with hard coatings such as TiCN and TiN on a high-performance high-speed steel substrate. Coated tools are not suitable for rough machining and high-impact interrupted cutting under heavy load and high hardness materials (such as hardened steel, chilled cast iron). When the coated tool is cut at a low speed, peeling, chipping, etc. are likely to occur. After the coated tool is reground, the coating effect is reduced. PM HSS In recent years, the industrialized countries have been vigorously developing powder metallurgy high-speed steels, which are high-speed steel powders directly obtained from high-pressure argon gas or pure nitrogen atomized molten high-speed steel molten steel, and then Hot isostatic pressing under high temperature and high pressure into steel ingots, and then made into high-speed steel. Compared with the high-speed steel produced by the fusion method, its advantages are: no carbide segregation, small and uniform grain size, up to 2 ~ 3μm, after heat treatment, hardness up to 67 ~ 70HRC, bending strength 0.5 ~ 1 times higher The high temperature hardness at 600°C is 2 to 3HRC higher. With the same cutting conditions, the tool life is increased by 0.5 to 2 times. Due to the isotropy of physical and mechanical properties, heat treatment deformation and stress can be reduced, making it suitable for manufacturing complex tools such as drills, broaches, and gear cutters. The cutting speed of such high-speed steel cutters can be doubled. After the surface PVD coating TiN, TiCN, TiAlN, the cutting speed can reach 150 ~ 200m/min. In the field of complex tool high-speed cutting, powder metallurgy high-speed steel coated tools will continue to develop and occupy an important position. 3 Challenges faced by domestic high-speed cutting tool materials The domestic high-speed cutting tool materials have a large gap with foreign countries. Currently, the tools used on imported and domestically produced high-speed machine tools mainly rely on imports. Therefore, high-speed cutting tool materials in China are facing severe challenges. At present, the most commonly used universal tool in China is mainly high-speed steel (W18Cr4V), which is mostly produced by smaller manufacturers. High-performance high-speed steels such as aluminum high-speed steel and cobalt high-speed steel have poor quality and are rarely used. Powder metallurgy high-speed steel cutters are still under research, cutting speed is generally 25 ~ 40m/min. Cars, routers, files, and end mills are generally used carbides, but most of them are welded knives, which are mainly hard alloys (TG, YT). Although the indexable insert has WC plus TaC, NbC or Hf-Nb, as well as ultra-fine carbide products, but the application is still not universal, the cutting speed is 100 ~ 200m/min. Hard alloys such as deep hole drills, thread cutters, etc. have products in recent years, but their application is less, and the processing efficiency is generally low. The most advantage of domestic high-speed cutting tools is ceramic tools. The level of research and development is equivalent to that of the international market. At present, there are more than 30 varieties of ceramic tools, of which there are more than 20 alumina bases and nearly 10 silicon nitride bases, including large and small ceramic cutters with holes. We have closely integrated cutting and tool material science for decades. After in-depth research, we have established a new ceramic cutting tool research system based on cutting reliability, fusion ceramic tool cutting theory and tool material research and development. It is now possible to optimize the cutting reliability and optimize the design to achieve superior performance of ceramic cutting tool materials. It is also advancing toward the international frontier of computer-aided design and hot-press process simulation of ceramic cutting tool materials. The traditional mode of research and development has accelerated the research and development of ceramic cutting tools. Based on this theory, we have successfully developed six varieties of 12 grades of Al2O3-based ceramic cutting tool materials, which have been put on the market, including aluminum-titanium (LT), whiskers (JX), boron-titanium (LP), and special powders. Rare earth LD series, gradient function (FG) and ceramic-hard alloy composite sheet (FH) series. The mechanical properties and wear and tear resistance of the FG and FH series have been significantly improved, extending tool life. JX-2, LP-2, gradient function FG, ceramic-hard alloy composite sheet (FH) and special powder-added LD-1, which are synthetically toughened by whiskers and granules in 6 varieties, not only fill the domestic gap, No report abroad. Domestic ceramic tool products have comparable mechanical properties and cutting performance to foreign countries, and some are better. Domestic ceramic cutters can turn or mill steel, alloy steel, cast iron, and alloy cast iron at a high speed of 300-1000 m/min. Among these Al2O3-based varieties, three types of SG-4, FG-2, and FH-2 are currently domestic High-speed processing of hardened steel (55 ~ 65HRC) ideal tool material. Domestic silicon nitride-based ceramic blades have excellent performance and show superiority in the machining of cast iron. Sialon ceramic knives also have products. The main difference between ceramic tools is that the accuracy and appearance quality of high-precision ceramic inserts are still poor, some varieties are not yet available, and popularization and application are far less popular than in developed countries. Cubic boron nitride (PCBN) for high-speed machining in China was successfully developed in 1973 and polycrystalline diamond (PCD) in 1980. It has developed rapidly and has been developed for use in various processing fields such as car, boring, and milling. PCBN tools with different CBN content and PCD tools with different grain sizes. Among them, PCBN tools are currently mainly used for machining hardened steels, hard cast irons, and certain difficult-to-machine materials. PCD tool is mainly used for high silicon aluminum alloy processing. At present, the superhard tools (PCBN, PCD, and natural diamond ND) that are mainly researched and produced by several domestic joint venture companies dominate the market. Two types of tool applications are not yet common. Synthetic single crystal diamonds and coated diamonds are still under study. Titanium carbide (TiC(N))-based hard alloys were developed in China in the late 1960s. The earliest was TiC-based hard alloys. In recent years, TiC(N)-based hard alloys containing TiN-containing TiC-TiN and TiCN have been successfully developed. Alloy several products, can be used for 200 ~ 400m/min high-speed precision and semi-finished steel, alloy steel and stainless steel. Recently, TiC+TiN nano-modified Ti(C,N)-based hard alloys with TiN nano-powders have been successfully developed. Tests have shown that 45 steels are machined at a speed of 200 m/min, which increases the life expectancy by a factor of two compared to tools without nano-modification. There is no product at present. The main problem with Ti(C,N)-based tool materials is that they have fewer varieties and are not used in many applications. Domestic development of coated tools began in the early 1970s. CVD TiC single-coated cemented carbides were initially developed. In the early 1980s, PCD TiN single coated high-speed steel tools were studied. After years of hard work. A number of coating equipments have been imported from abroad. In recent years, CVD TiC-TiN, Al2O3-TiN multi-coated cemented carbide inserts and PVD TiN, TiCN, TiAlN, TiAlCN composite high-speed steel complex cutters have been successfully developed. Low-temperature (<600°C) external heat type DC pulsed plasma enhanced chemical vapor deposition (PCVD) technology has also been successfully developed. It has the advantages of simple equipment, uniform coating thickness, high bonding strength, multiple types of coating materials, and no deformation of the workpiece. . However, the main products currently on the market for coating tools are CVD Al2O3 and TiN composite coated carbide inserts and PVD TiN coated high-speed steel cutting tools. TiCN, TiAlN and TiAlCN commercial coating products are difficult to supply in time because of technical reasons, and there is still a gap between quality and abroad. PVD hard coatings such as carbon nitride (CNx), Al2O3, nitride [TiN (NbN), TiN/VN, etc.] and diamond PCD film coatings and soft coatings (MoS2, WS2) and nano-coatings etc. to be developed . Foreign companies in the country are selling hot-selling coated tools, which has hit the domestic market. 4 Future of high-speed cutting tool materials The goal of ultra-high-speed cutting is: milling aluminum 10000m/min, cast iron 5000m/min, ordinary steel 2500m/min: and drilling aluminum, cast iron and ordinary steel respectively 30000, 20000 and 10000r/min. Therefore, in the future, it is necessary to develop tool materials that have better high-temperature mechanical properties, high chemical stability, thermal stability, and high thermal shock resistance. PCD cutters will continue to develop and improve performance. They are widely used in the processing of aluminum alloys and high hardness non-metallic materials, but synthetic synthetic single crystal diamond and diamond thick film coatings will develop faster and will gradually replace PCD, depending on the cost. In the field of high-speed ultra-precision mirror cutting, natural diamond tools still play an important role, but some will be replaced by artificial single crystal diamond. At present, the main limitation of PCD cutting tool machining aluminum alloy cutting speed is the spindle speed and power of the machine tool. Al2O3-based and Si3N4-based ceramic tools and CBN tools are the preferred tool materials for high-speed cutting steel, cast iron and their alloys, but each has its scope of use and should continue to develop. Al2O3-based ceramic cutting tools have a wider application prospect for high-speed machining steels and their alloys. Compared with CBN cutting tools, they have both cost advantages and are suitable for machining hardened steel and unhardened steel and ferrite materials, but heat-resistant. Sex and thermal shock resistance are not enough. The development of nano-composite Al2O3-based ceramic tools with CBN added to CBN to develop high-temperature strength and thermal shock resistance at temperatures above 1400-1500°C is the main direction for the future. The development of Al2O3+Si3N4-based CBN-based composite tool materials with higher high-temperature strength and chemical stability in the high-speed processing of heat-resistant alloys is an important research direction. Coating tool materials have great potential in the field of high-speed cutting, continue to study new coating technologies and coating materials, improve performance, and expand use. However, the development of powder coating, a new generation of coating tools that coat high-performance wear-resistant materials on cemented carbide and powdered high-speed steel powders (grains), can be reground without affecting the performance of complex tooling. Particularly meaningful. Our successfully developed coating blades coated with Al2O3 on hard alloy powder illustrate its feasibility and superiority. For some workpiece materials that are difficult to process and have many applications (such as titanium alloys), because of their cutting, even at medium speeds, the temperature is very high, and the study does not pollute the environment of air-cooled (such as nitrogen) methods to reduce cutting Temperature to achieve efficient cutting is a feasible and promising direction. 5 Conclusion High-speed cutting technology has become the mainstream of cutting processing. Accelerating its promotion and application will create tremendous economic benefits. High-speed cutting tool materials play a decisive role in the development and application of high-speed cutting technology. Superhard cutting tool materials (PCD and .CBN), ceramic cutting tools, TiC(N)-based carbide cutting tools (cermets), and coated cutting tools have four major types of high-speed cutting tool materials, each with its own characteristics and application range. , compete with each other to promote the development and application of high-speed cutting technology. Domestically, there is also a certain foundation in this respect, and great progress has been made. In particular, China has a prominent advantage in ceramic cutting tools, but generally speaking, it has a large gap with foreign countries. We seize the great opportunity of economic globalization and reform and opening up and bravely face the severe challenges we face. While using foreign mature technologies in different ways to speed up the development of China's high-speed cutting tool material industry, we will focus on the development of a new generation of ceramic-based CBN composite tool materials and coated tool material technologies to promote high speed and ultra-high speed in China. The rapid development and application of cutting technology.
G-series
LPG&Gasoline Forklift:
G-series LPG&Gasoline Forklift is one
kind of Internal Combustion Forklift,the power is LPG or both.LPG &
Gasoline combustion fully, improve the life of engine three times.
The advantages include:
1.More
environmental protection than diesel forklift.
2.Excellent
wide view mast.
3.Robot
welding chassis.
4.Quality
Korea brand KCC painting.
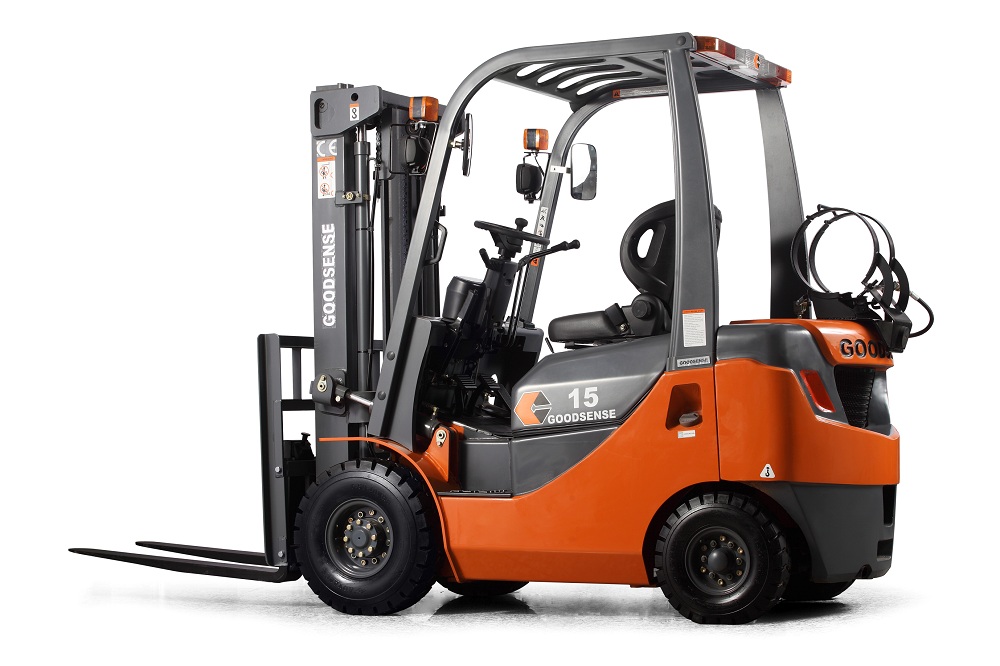
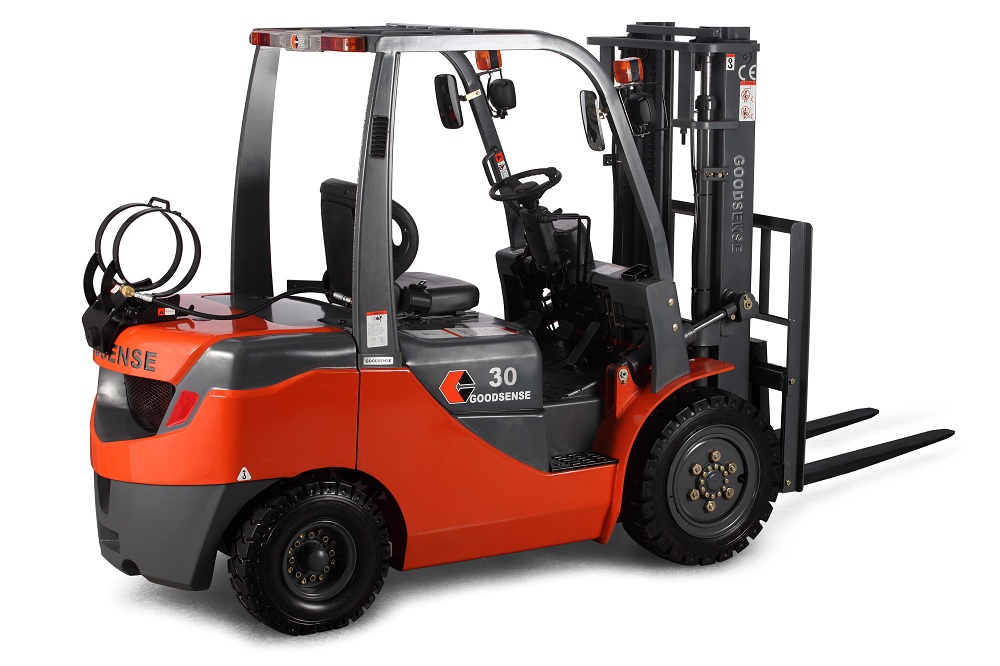
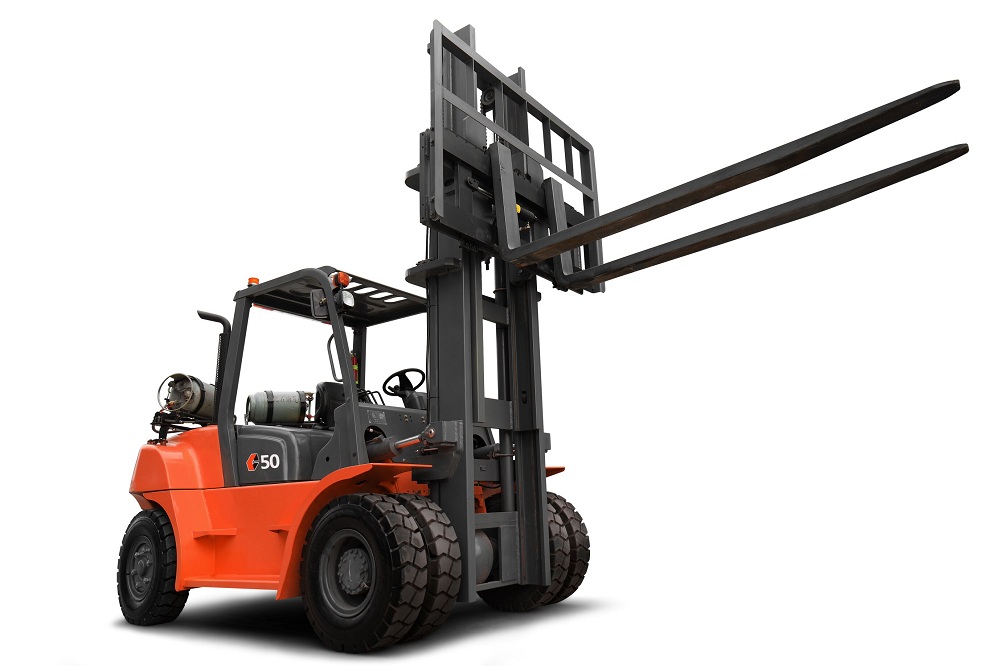
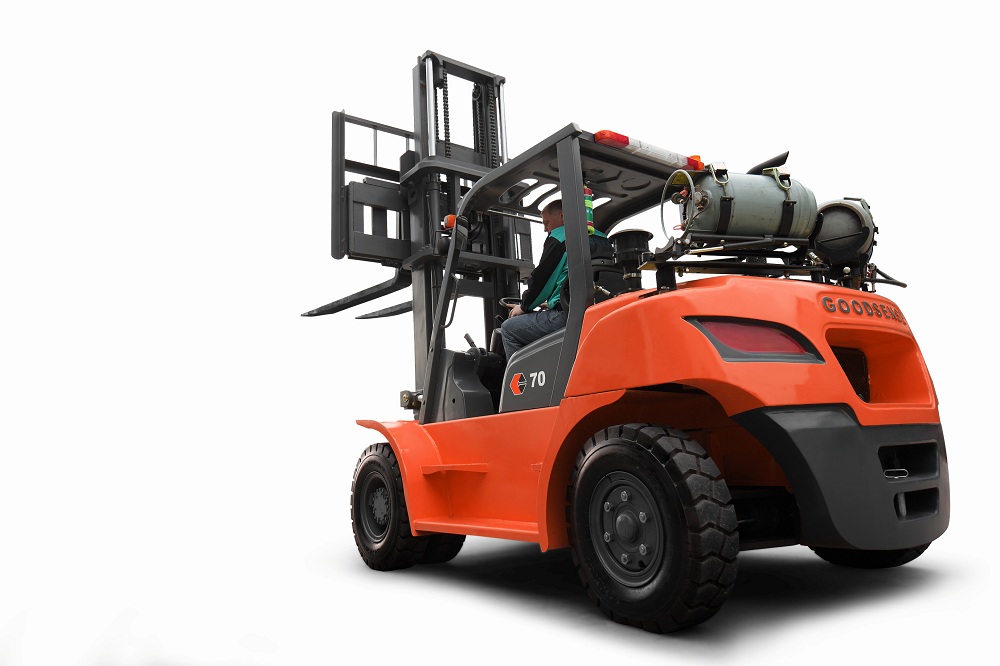
Application Area:
1.Warehouse
2.Port
3.Factory
4.Distribution
Center
5.Logistics
If you have any other questions,please
contact us directly.Our forklift are all with high quality,and you can choose
any other engine to equip.It can be produced according to your idea.And we
invite you to visit our factory.
G-series LPG&Gasoline Forklift
G-series LPG Forklift,Gasoline Forklift,LPG&Gasoline Forklift,1.8Ton LPG&Gasoline Forklift
ZHEJIANG GOODSENSE FORKLIFT CO.,LTD , https://www.dieselforklift.nl