I. INTRODUCTION In recent years, with the vigorous development of national construction, hoists have become more and more widely used in electric power construction, water conservancy construction and transportation ports. When the hoist is lifting a relatively wide gate, the single hoisting point cannot meet the requirements for the opening and closing of the gate. At this time, we must use the double hoisting point structure type hoisting machine to lift the gate.
The square V560 series high-performance closed-loop vector inverter can realize high starting torque and ultra-low speed operation. This article mainly introduces how to successfully apply the V560 series inverter to the master-slave control of the double hoisting hoist.
Second, the system overview An example of a hoist in a hydropower station in Jiangmen, the scene is a 2×1500KN fixed winch hoist, using a double-lift point structure, driven by two sets of Φ900mm diameter reels. Heavy spreader. Each set consists of a 75kW electric motor driven by a hardened surface bedroom reducer. The two sets of mechanisms are coupled through a coupling and a rigid shaft to maintain the synchronism of lifting of the two hoisting points. Two sets of mechanisms are controlled by a hydraulic brake.
Due to the slip characteristics of the asynchronous motor in the electrical system, when two or more motors drive a rigid load at the same time, uneven load distribution occurs. In severe cases, a motor may even be pulled under light load conditions. Another motor works, one motor is in an electric state, and one motor is in a state of power generation. In order to avoid this, the load of each hoisting point of the hoist is evenly distributed. The hoisting machine of each hoisting point of the double hoisting hoist adopts the frequency conversion master-slave control method, which can solve the above problems well.
Third, the system control program and configuration hoist two hoisting institutions using Quartet V560 high-performance vector inverter, two inverters are used closed-loop vector control, the main inverter speed control, torque control from the inverter, the main The two analog AO1 and AO2 output terminals of the inverter output the frequency command and torque command respectively, the frequency command uses 0~10V signal, and the torque command uses -10V~10V signal. From the AI1 terminal of the inverter, the output signal of the AO1 terminal of the main frequency conversion is accepted as the speed limit, and the AO2 terminal output signal of the host inverter is accepted as the torque command from the AI3 terminal of the inverter. When starting work, the main frequency converter drives the load to generate an actual internal torque command, and this torque command is output to the slave frequency inverter that is used as the torque control, and the slave inverter will also output a torque of the same size. In this way, the output torque of the two inverters is the same, and there will be no load imbalance. The frequency inverter of the main frequency converter is output to the slave inverter as the speed limit, so the speed of the slave inverter is limited to the current running speed of the master inverter.
Electrical wiring diagram shown in Figure 1:
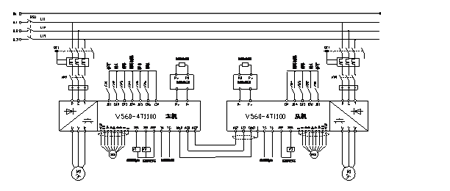
Fig. 1 Principle diagram of the master-slave inverter main circuit IV. Commissioning steps Before setting the parameters of the inverter, first perform the static inverter self-learning, and then set the corresponding parameters to the corresponding inverter after self-learning. Inverter parameters:
Table 1: Frequency converter parameters
Note: The parameters that are not specified in the Remarks column are the parameters that the master and slave inverters must set. The remarks are the parameters that the master and slave inverters need to set.
V. Notes on debugging If the output torque of the master-slave inverter is inconsistent during the debugging, the value of the analog AI3 from the inverter needs to be corrected according to the actual situation. The correction method is: query d1.0.05 analog input AI3 value, and d1. The value of 0.05 is written in the parameter analog input AI3 curve correction value F4.1.19. Query d0.0.09 again, and the output torque of the inverter is 0.0%.
Determine the master-slave control parameter debugging method, start the lifting mechanism for a period of time, use the infrared thermometer to test the main and the inverter braking resistor temperature, if the temperature deviation is not large, it means that the inverter master-slave control parameters have been adjusted Good, but not vice versa. Can also be viewed by the master and slave frequency converter torque output monitoring parameters d0.0.03, if the values ​​are the same or similar, it indicates that the frequency converter master-slave control parameters have been adjusted.
VI. Summary The successful application of the Quartet V560 high-performance vector inverter on a fixed winch at a double hoisting point of a hydropower station solved the problem of uneven load distribution when two or more motors are driving a rigid load at the same time. A phenomenon occurs where one motor drags another motor. After on-site testing, the entire system is stable, easy to use, and effective. It is well received by users.
The square V560 series high-performance closed-loop vector inverter can realize high starting torque and ultra-low speed operation. This article mainly introduces how to successfully apply the V560 series inverter to the master-slave control of the double hoisting hoist.
Second, the system overview An example of a hoist in a hydropower station in Jiangmen, the scene is a 2×1500KN fixed winch hoist, using a double-lift point structure, driven by two sets of Φ900mm diameter reels. Heavy spreader. Each set consists of a 75kW electric motor driven by a hardened surface bedroom reducer. The two sets of mechanisms are coupled through a coupling and a rigid shaft to maintain the synchronism of lifting of the two hoisting points. Two sets of mechanisms are controlled by a hydraulic brake.
Due to the slip characteristics of the asynchronous motor in the electrical system, when two or more motors drive a rigid load at the same time, uneven load distribution occurs. In severe cases, a motor may even be pulled under light load conditions. Another motor works, one motor is in an electric state, and one motor is in a state of power generation. In order to avoid this, the load of each hoisting point of the hoist is evenly distributed. The hoisting machine of each hoisting point of the double hoisting hoist adopts the frequency conversion master-slave control method, which can solve the above problems well.
Third, the system control program and configuration hoist two hoisting institutions using Quartet V560 high-performance vector inverter, two inverters are used closed-loop vector control, the main inverter speed control, torque control from the inverter, the main The two analog AO1 and AO2 output terminals of the inverter output the frequency command and torque command respectively, the frequency command uses 0~10V signal, and the torque command uses -10V~10V signal. From the AI1 terminal of the inverter, the output signal of the AO1 terminal of the main frequency conversion is accepted as the speed limit, and the AO2 terminal output signal of the host inverter is accepted as the torque command from the AI3 terminal of the inverter. When starting work, the main frequency converter drives the load to generate an actual internal torque command, and this torque command is output to the slave frequency inverter that is used as the torque control, and the slave inverter will also output a torque of the same size. In this way, the output torque of the two inverters is the same, and there will be no load imbalance. The frequency inverter of the main frequency converter is output to the slave inverter as the speed limit, so the speed of the slave inverter is limited to the current running speed of the master inverter.
Electrical wiring diagram shown in Figure 1:
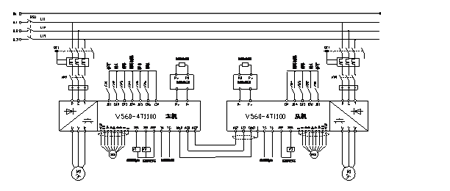
Fig. 1 Principle diagram of the master-slave inverter main circuit IV. Commissioning steps Before setting the parameters of the inverter, first perform the static inverter self-learning, and then set the corresponding parameters to the corresponding inverter after self-learning. Inverter parameters:
Table 1: Frequency converter parameters
2×70T Lifting Mechanism Master-slave Control Frequency Converter Parameters
parameter name
Factory setting value Remarks F0.0.09 Control mode selection 0000 0010 F0.2.25 Frequency setting channel 2 2/9 Master/Slave F0.2.29 Panel digital setting 0.0 10.0 F0.3.33 Control command 0 1 F0.4.39 Starting frequency 0.5 1.5 F0.4.40 Starting frequency holding time 0.0 0.5 F1.0.03 Acceleration time 20 5 F1.0.04 Deceleration time 20 3 F1.0.11 Emergency stop deceleration time 10 3 F3.0.00 Input terminal DI1 function selection 0 7 F3.0.01 Input terminal DI2 function Selection 0 8 F3.0.02 Input terminal DI3 function selection 7 14 F3.0.03 Input terminal DI4 function selection 8 13 F3.0.04 Input terminal DI5 function selection 13 1/0 Master/Slave F3.0.05 Input terminal DI6 function selection 0 2/0 Master/Slave F3.1.12 Output terminal DO1 function selection 1 4 Main inverter F3.1.13 Output terminal DO2 function selection 1 2 F3.1.21 Relay output function selection 4 71/4 Master/slave F4.2.23 Output terminal AO2 Mapping variable 2 3 F6.0.00 1st operating frequency 5.00 30.00 Main frequency converter F6.0.01 2nd operating frequency 10.00 50.00 Frequency converter F8.3.39 Selection of torque control mode 0 1 Selection of frequency converter from F8.3.40 torque command channelNote: The parameters that are not specified in the Remarks column are the parameters that the master and slave inverters must set. The remarks are the parameters that the master and slave inverters need to set.
V. Notes on debugging If the output torque of the master-slave inverter is inconsistent during the debugging, the value of the analog AI3 from the inverter needs to be corrected according to the actual situation. The correction method is: query d1.0.05 analog input AI3 value, and d1. The value of 0.05 is written in the parameter analog input AI3 curve correction value F4.1.19. Query d0.0.09 again, and the output torque of the inverter is 0.0%.
Determine the master-slave control parameter debugging method, start the lifting mechanism for a period of time, use the infrared thermometer to test the main and the inverter braking resistor temperature, if the temperature deviation is not large, it means that the inverter master-slave control parameters have been adjusted Good, but not vice versa. Can also be viewed by the master and slave frequency converter torque output monitoring parameters d0.0.03, if the values ​​are the same or similar, it indicates that the frequency converter master-slave control parameters have been adjusted.
VI. Summary The successful application of the Quartet V560 high-performance vector inverter on a fixed winch at a double hoisting point of a hydropower station solved the problem of uneven load distribution when two or more motors are driving a rigid load at the same time. A phenomenon occurs where one motor drags another motor. After on-site testing, the entire system is stable, easy to use, and effective. It is well received by users.
Gleey , https://www.geelygroups.com