1 The basic idea of ​​the mathematical model The shape of the tooth profile of the non-circular gear is not only related to the relative motion parameters of the workpiece and the tool, but also to the tooth profile of the tool.
When machining with a rack tool, since the tooth angles of the points on the tooth profile of the rack tool are constant values, the pair of non-circular gear pairs that are machined can obviously perform the correct meshing transmission according to the known pitch curve.
Knowing the non-circular gear section curve, according to the involute gear tooth profile forming principle, the idea of ​​machining the gear by means of the gear shaping method--when a pair of conjugate tooth profiles mesh with each other, the tooth profiles are envelops with each other. The involute cylindrical gear indexing circle is purely rolled on the non-circular gear section curve, and the tooth profile of the cylindrical gear (pinning cutter) envelops the tooth profile of the non-circular gear.
Therefore, it is first necessary to establish the mathematical model of the involute cylindrical gear profile of the shaper cutter, and then establish the geometric positional relationship between the insert and the non-circular gear blank as a knot curve, so that it can be purely rolled. The meshing equation combines the two models to obtain a mathematical model of the non-circular gear profile curve.
2 The establishment of the conjugate tooth profile equation 2.1 The formation of the involute is as shown in 1. When the straight line AB is tangent-rolled along the circumference, any point K on the line AB is called the track K0K on the plane fixed to the circle. For the involute of the circle. This circle is called the base circle of the involute, its radius is represented by Rb, the line AB is called the occurrence line of the involute, and the angle θK is the angle of the involute K0K.
2.2 The mathematical equation of the involute curve of the incisor is shown in Fig. 1. If the vector of the involute starting point K0 is OK0, the axis of the arbitrary diameter K of the involute is clipped to the polar axis. The polar angle is the polar angle, and the polar coordinate equation at any point on the involute is:
invαK=θK=tanαK-αKRK=RbcosαK(1) The calculation of the tooth thickness on an arbitrary circle is as shown in 2, KK′ is the tooth thickness of the arbitrary circle on the involute, and is represented by SK; S is the index circle. The tooth thickness; θK and θ are the angles of the involute at the point K of the arbitrary circle and the point C of the index circle, respectively.
2 The tooth thickness on the arbitrary circle is the tooth thickness formula on the arbitrary circle of the involute gear: SK=SRKR-2RK(invαK-invα) (2) where S and α are the tooth thicknesses on the index circle, respectively. Pressure angle; SK, αK are the tooth thickness and pressure angle on an arbitrary circle respectively; βK is the half angle of the center corresponding to SK, βK=SK/(2RK); therefore the coordinates of point K are:
xK=RKcos(π/2-βK)yK=RKsin(π/2-βK) (3) Equation (3) is the basic mathematical equation of the involute profile curve of the shaper cutter.
2.3 The positional relationship between the pinion cutter and the non-circular gear establishes the positional relationship between the pinion cutter and the non-circular gear (as shown in 3). The pinion cutter is an involute spur gear. When machining, the center of rotation of the pinion cutter starts from the farthest point at the center of rotation of the non-circular gear, and the pitch circle and the non-circular gear section curve are tangent to point P, and are not round. Pure rolling on the gear section curve, that is, the fan motion. The distance between the center of rotation O2 of the shaper and the center of rotation O1 of the non-circular gear is set to R, and the angle with the horizontal line is α. The polar coordinates of the tangent point P on the knot curve are expressed as Ï and a polar angle of φ. Since the non-circular gear section curve is an arbitrary curve, and the tool section curve is a circle, the tangent point of any curve and the circle is not on the concentric line of the two, so the actual non-circular gear (blank) rotation angle is not the inter-cutting arc The length corresponds to the polar angle φ, but α.
3 Mathematical model of non-circular gear tooth profile The tooth profile mathematical model is established by machining mathematical model, and the involute non-circular gear tooth profile is enveloped by the meshing principle.
3.1 The mathematical model of the driving wheel profile machining is based on the positional relationship between the center of the indexing circle and the non-circular gear section curve, and the meshing equation is established as follows: α=φ-α' arctanm(4) where α' is The mid-mesh point tangent line CP and R are surrounded by a right-angled triangle O1 point.
m=cotμ, μ=π2 (α α'-φ) During the machining process, the arc length of the tool rolling on the tooth section curve should be equal to the arc length of the tool rotating around its own center of rotation O2, thus ensuring the tool and teeth. The relationship between the billets. However, the tangent point of the shaper blade and the tooth blank curve is not on the concentric line of the two, so the actual rotation angle of the tool is not the central angle β of the corresponding arc length ΔS, but Ψ, then Ψ=β-β'.
ΔS=∫φ ΔφφÏ2 (dÏdφ)2dφ=β180Ï€R204
Where β = ΔSR2180π. Because β'=α', there are: Ψ=ΔSR2180π-α' (5) At the same time, we should also consider ensuring that there are integer teeth on the curve, and further determine some characteristic coefficients in the section curve. The calculation formula is :
S=∫2Ï€0Ï2 (dÏdφ)2dφ=Ï€mz(6)
3.2 Mathematical model of the driven wheel profile According to the condition that a pair of non-circular gear pairs can be correctly meshed, after the driving wheel is processed, the positional relationship between the pinion cutter and the driven wheel can be determined according to the pitch curve equation of the driven wheel. At the same time, according to the requirements of machining a pair of non-circular gears, after the driving gear is machined, the tool teeth can be returned to the original state, and then the gear is rotated by one-half of the pitch, and then the driven wheel is started. The rotation angle γ is:
γ=πm2R2π180(7)
3.3 Mathematical model in the computer simulation of the tooth profile is different from the actual machining of the non-circular gear. In actual machining, the workbench will drive the workpiece to make a rotary motion on the one hand, and maintain the center distance change with the shaper cutter on the other hand, that is, to make a translation. However, if you want to obtain the profile of the tooth profile by means of computer graphics simulation, you need to assume that the workpiece does not move. The shaper cutter rolls around the workpiece on its section curve and guarantees: 1 the instantaneous angular velocity of the workpiece and the instantaneous angular velocity of the tool Meet the requirements of the instantaneous transmission ratio; 2 Ensure that the center of the workpiece and the center of the shaper cutter change according to the established variation of the center distance.
This is the result of the tooth profile of the workpiece.
This paper starts from the processing method, based on the theory of non-circular gears of the shaper cutter, constructs the mathematical model of non-circular gear machining, and simplifies the method of non-circular gear tooth profile design. This method is not only suitable for non-circular gears with convex curve, but also for non-circular gears with concave curve and also for non-circular gear design of closed and non-closed joint curves.
EVA Traction Pad is the tail pad to be sticked on the surfboard. It comes with center arch and kick tail, which allow surfers to control the direction and stability when surfing in the sea.
The design of surfboard traction pad can be in one piece, two pieces, or three pieces basically. The standard the classical texture for traction pad would be diamond like texture, as it can provide the stronger grip among all of them.
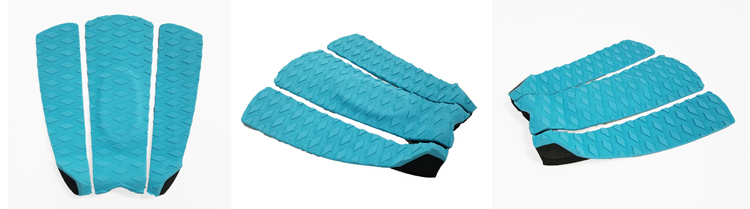
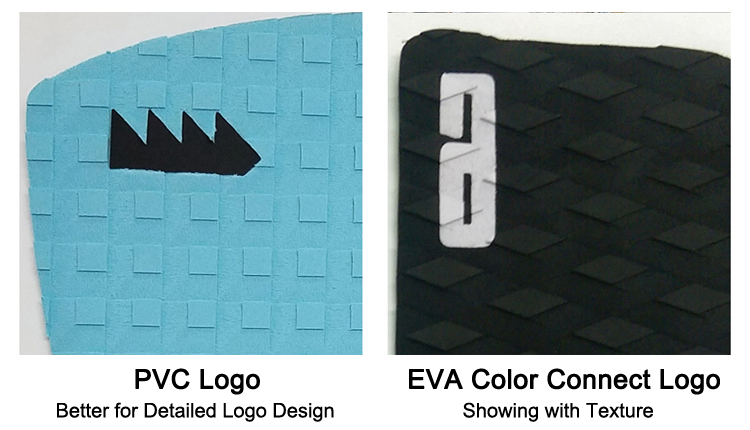
The EVA color connect logo is made along with the pad itself. Unlike the PVC logo, it is also EVA material same as pad, and also shows with the texture. The design of this logo can not be too detailed and small, it needs to be larger and simpler so that we can use the different color EVA material to connect them.
Eva Traction Pad,Non-Skip Traction Pad,Traction Pad,Surfboard Tail Pads,Grip Tail Pad,Eva Tail Pad
Huizhou City Melors Plastic Products Co., Limited , https://www.foamexpert.net